
The fine-grained, homogenous microstructure was observed, where cracks and voids were identified only for films with high Co-content. A comprehensive analysis of the structural properties (performed with GIXRD and SEM) revealed the amorphous nature of (Ti,Co)Ox coatings, regardless of the cobalt content in the coating. Moreover, the deposition rate under neutral conditions (in Ar plasma) was even 10-times higher compared to oxidizing Ar:O2 (70:30) plasma. There was 15–20% more cobalt in the films than in the target. The relation between the Ti–Co target composition and the Co-content in the metallic and oxide films was examined. The deposition was carried out from sintered targets with different Co-content (2 at.%, 12 at.% and 50 at.%). Thin-film coatings were prepared using the magnetron sputtering method. In this work, selected properties of metallic and oxide thin films based on titanium and cobalt were described. hardness:elastic modulus ratio (higher for sequential process) and corrosion resistance (better for sequential process). Significant differences were observed in porosity (lower for sequential process), scratch resistance (better for sequential process), mechanical performance, i.e. Deposited coatings had high transparency in the visible wavelength range. Both films exhibited nanocrystalline anatase structure with crystallite sizes of ca.
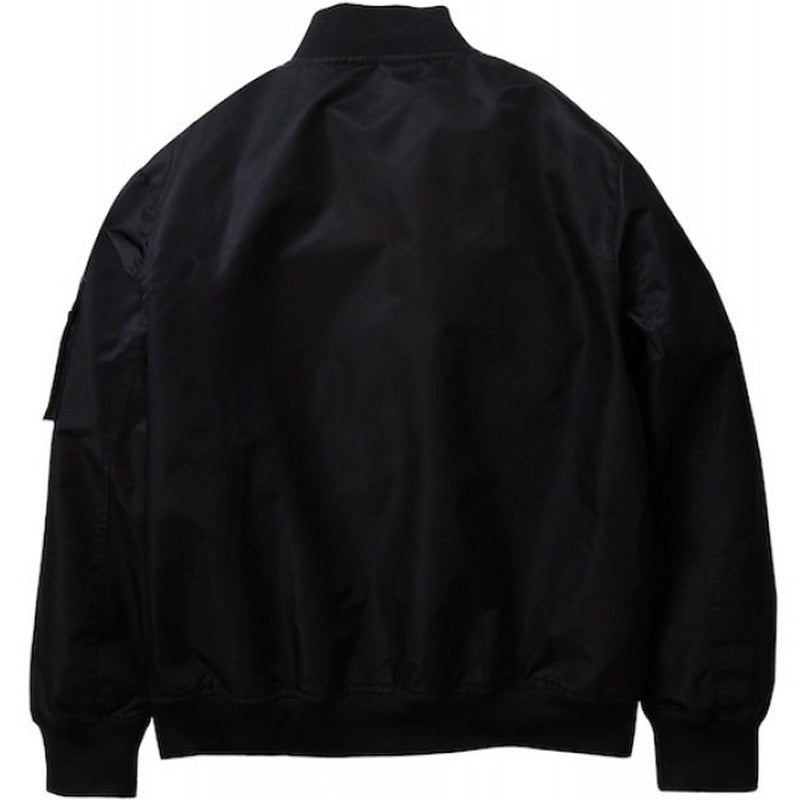
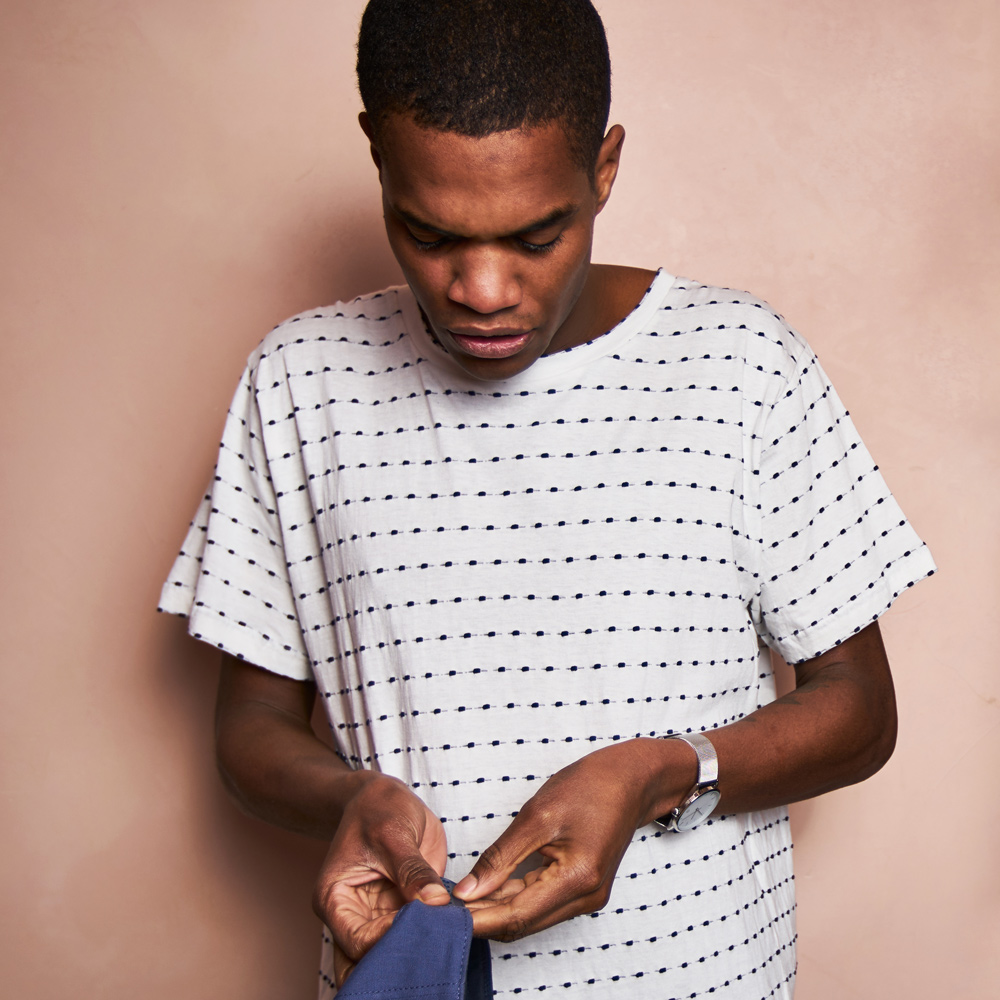

Structural analysis showed that there were no major differences in the microstructure between coatings deposited in continuous and sequential processes.
#TEXTIFY MODU T JACKET CRACK#
The TiO 2 thin films were crack free, exhibited good adherence to the substrate and the surface morphology was homogeneous. In turn, in sequential process, the voltage was supplied for 1 s alternately with 1 s break, therefore, the total time of the process was extended to 180 min. In case of continuous process, magnetron was continuously supplied with voltage for 90 min. In this paper, comparative studies on the structural, surface, optical, mechanical and corrosion properties of titanium dioxide (TiO 2 ) thin films deposited by continuous and sequential magnetron sputtering processes were presented.
